Understanding Plastic Mold Tools: A Comprehensive Guide for Metal Fabricators
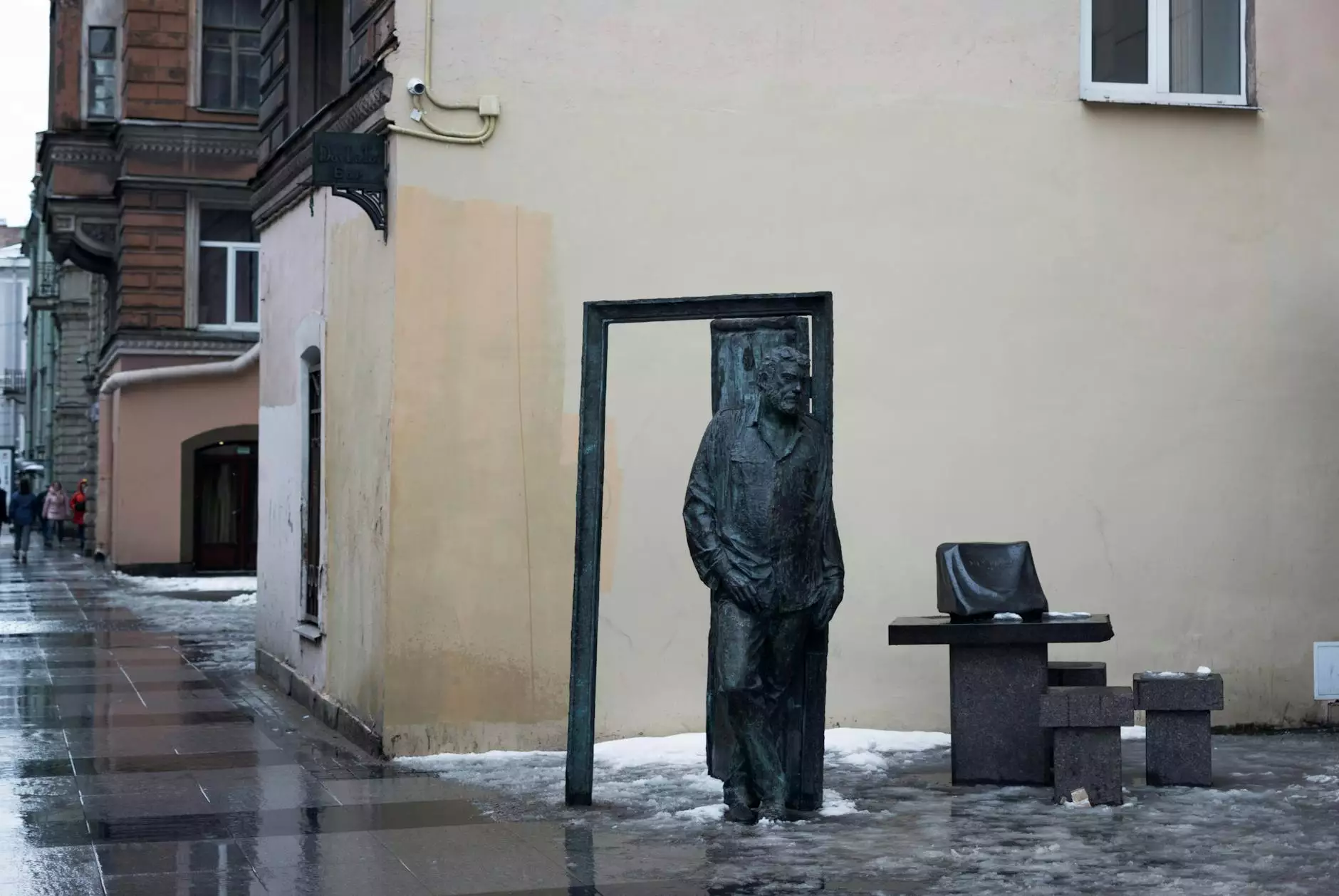
In the ever-evolving industrial landscape, the importance of plastic mold tools cannot be overstated. These tools serve as pivotal components in the manufacturing and design processes across various industries, particularly for metal fabricators. In this detailed article, we will delve deep into the world of plastic mold tools, examining their utility, the benefits they bring to businesses, and how companies like DeepMould.net leverage them to meet and exceed client expectations.
The Role of Plastic Mold Tools in Manufacturing
Plastic mold tools are essential devices used to create objects made of plastic through the injection molding process. These tools consist of two primary parts: the mold cavity, where the liquid plastic is injected, and the core, which shapes the exterior of the product. The precise engineering of these molds directly influences the quality, performance, and longevity of the final product. Let’s explore some of the key functions of plastic mold tools.
1. Creating Complex Shapes
One of the most significant advantages of using plastic mold tools is their ability to produce highly detailed and complex shapes. This flexibility allows metal fabricators to create intricate designs that would otherwise be challenging and costly to manufacture using traditional methods.
2. High Volume Production
Plastic mold tools allow for rapid and efficient production runs. Once the mold is created, it can produce thousands of identical items with minimal variations, making it ideal for high-volume production scenarios.
3. Cost-Effective Manufacturing
While the initial investment in creating plastic mold tools can be significant, the overall cost-effectiveness is unparalleled in long-term production. The ability to mass-produce high-quality parts reduces the cost per unit, making it an economical choice for metal fabricators.
4. Enhanced Product Quality
The precision of plastic molds contributes to the high quality of the finished products. A well-designed mold ensures that there are fewer defects and that the final goods meet the desired specifications.
Types of Plastic Mold Tools
There are various types of plastic mold tools used in the industry, each designed for specific applications. Below are some common types:
- Injection Molds: Used for injecting molten plastic into a mold cavity, ideal for mass production.
- Blow Molds: Primarily used for hollow objects, these molds involve inflating a heated plastic tube.
- Thermoforming Molds: Utilized in heating plastic sheets and forming them over mold shapes, suitable for low-cost applications.
- Compression Molds: Used in creating complex parts by pressing plastic material into the mold cavity under high pressure.
Choosing the Right Plastic Mold Tools
For metal fabricators, selecting the appropriate plastic mold tools is crucial for optimizing production efficiency and product quality. Here are some factors to consider:
1. Material Compatibility
It is essential to select molds that are compatible with the type of plastic being used. Different plastics have different properties and require molds that can withstand specific temperature ranges and chemical compositions.
2. Production Volume
The expected production volume plays a significant role in determining the type of mold. For high-volume production, investing in high-quality injection molds may yield the best returns.
3. Design Complexity
Complex designs may require advanced mold-making techniques, such as multi-cavity molds, to ensure efficiency in production. Understanding the design requirements upfront helps in making informed decisions.
4. Budget Considerations
While high-quality molds can be expensive, it’s essential to factor in the long-term benefits. A well-made mold will reduce maintenance costs and enhance production efficiency, making it a worthwhile investment.
Benefits of Using Plastic Mold Tools in Metal Fabrication
The utilization of plastic mold tools offers several advantages to businesses in metal fabrication:
1. Increased Efficiency
With the ability to produce parts rapidly and accurately, businesses can meet tight deadlines and fulfill large orders without compromising quality.
2. Reduction in Waste
By leveraging precision molds, fabricators reduce the amount of scrap material generated during production, contributing to more sustainable manufacturing practices.
3. Customization Opportunities
Plastic molds can be designed to incorporate specific brand logos or custom features, allowing businesses to create unique products that stand out in the marketplace.
4. Improved Safety and Ergonomics
Modern plastic mold tools are designed with user safety and ergonomics in mind, reducing risks associated with manual handling and improving overall workplace safety.
The Process of Creating Plastic Mold Tools
The process of designing and manufacturing plastic mold tools involves several critical steps:
1. Design and Prototyping
Initially, engineers create a CAD (Computer-Aided Design) model of the part that is to be produced. Prototyping enables testing of design feasibility and functionality before finalizing the mold design.
2. Material Selection
The choice of materials for the mold is crucial, as they must withstand high pressures and temperatures. Common materials include steel and aluminum, each with its own set of advantages.
3. Machining the Mold
The actual creation of the mold involves machining techniques like CNC (Computer Numerical Control) milling and electrical discharge machining. This step requires precision to ensure the exact specifications of the mold are met.
4. Assembly and Testing
Once the mold components are machined, they are assembled and undergo rigorous testing to ensure they function correctly under real production conditions.
Future Trends in Plastic Mold Tooling
The future of plastic mold tools looks promising, with several emerging trends shaping the industry:
1. Advanced Materials
The development of new materials for molds enhances durability, cost-effectiveness, and the ability to produce more complex shapes.
2. Automation and AI Integration
Automation in the design and production processes is on the rise, reducing lead times and allowing for real-time adjustments based on production demands.
3. Sustainability Practices
As industries strive for eco-friendliness, the creation of molds that utilize recycled materials is expected to gain momentum.
4. Industry 4.0 Revolution
The integration of IoT (Internet of Things) technology into mold production processes will enable smarter factories where machine performance can be monitored and optimized in real time.
Conclusion
In summary, plastic mold tools play a vital role in the manufacturing landscape, particularly for industries relying on metal fabrication. Their ability to produce high-quality, intricate designs efficiently and cost-effectively positions them as an indispensable asset for businesses like DeepMould.net. As technology continues to advance, the potential for innovation in plastic mold tooling is immense, promising a future of enhanced production capabilities and greater sustainability.
Engaging with high-quality mold tools not only enhances product quality but also fosters business growth and improves customer satisfaction. Therefore, investing in well-engineered plastic mold tools should be a strategic priority for any metal fabricator looking to thrive in today's competitive environment.