Understanding Injection Plastics and Their Impact on Metal Fabrication
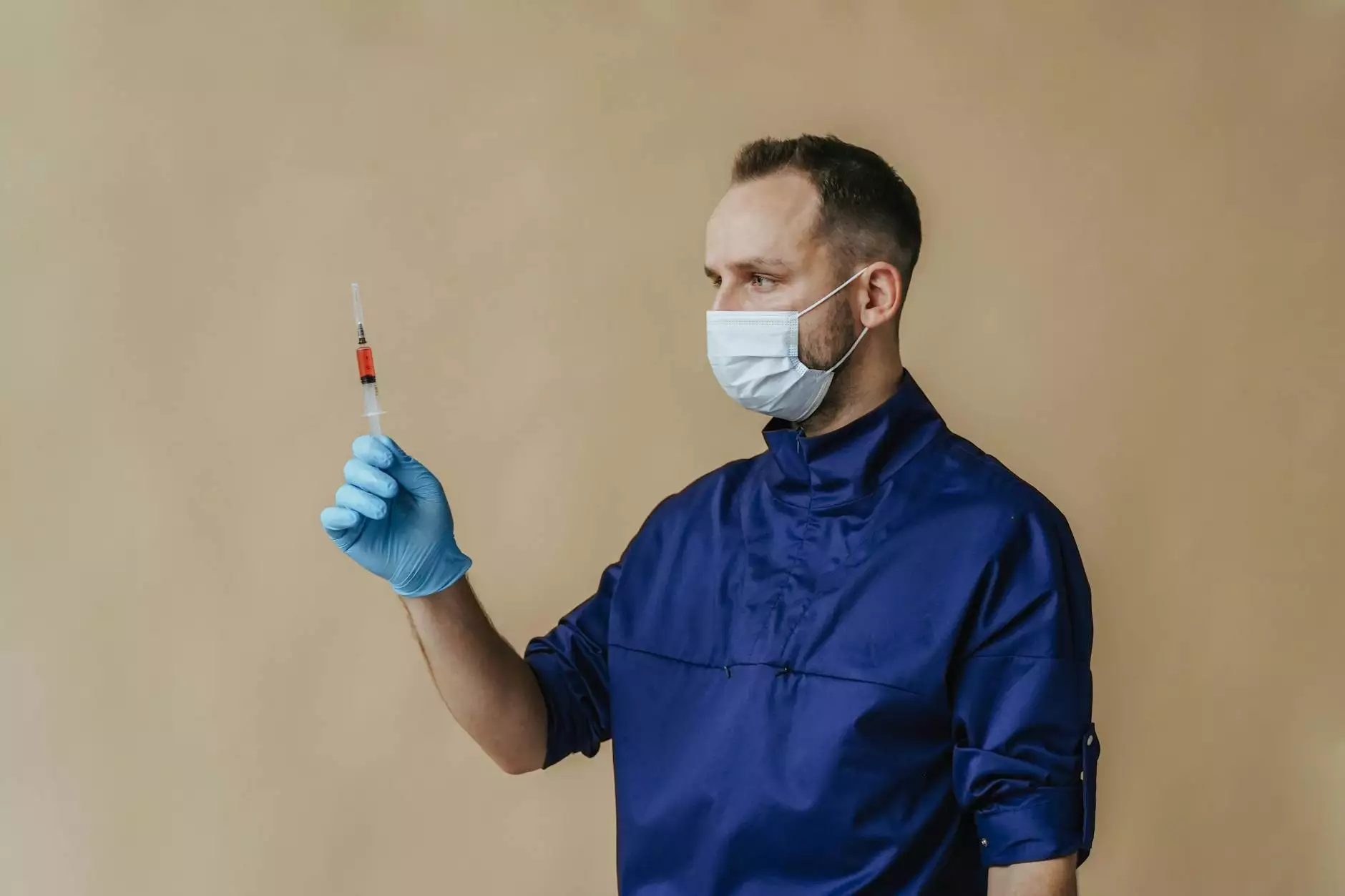
Injection plastics have emerged as a pivotal technology within the manufacturing sector, especially in the realm of metal fabrication. As industries evolve to meet rigorous demands for efficiency, accuracy, and sustainability, understanding the role of injection plastics becomes essential. In this article, we will delve deep into what injection plastics are, their applications, benefits, and how they are influencing the future of metal fabrication, particularly in the context of deepmould.net.
What are Injection Plastics?
Injection plastics refer to a process of shaping materials, primarily thermoplastics, by injecting them into a mold under pressure. This technique allows the production of complex shapes with high precision. The process involves several key stages:
- Material Preparation: The raw plastic material is first fed into a heated barrel where it is melted.
- Injection: The molten plastic is then injected into a mold cavity at high pressure.
- Cooling: Once the mold is filled, the material is allowed to cool, solidifying into the desired shape.
- Demolding: Finally, the mold is opened, and the finished product is ejected.
The Benefits of Injection Plastics in Metal Fabrication
The integration of injection plastics in metal fabrication offers a myriad of advantages, making it a go-to choice for manufacturers. Here are some of the key benefits:
- Cost Efficiency: Injection molding is highly efficient, significantly reducing material waste compared to other methods. This translates to lower production costs and a more sustainable approach to manufacturing.
- High Precision: Injection plastics enable the creation of complex components with meticulous detail, ensuring that metal parts fit perfectly in assemblies, enhancing overall quality.
- Speed of Production: The injection process is fast, allowing for high-volume production without sacrificing quality. This is crucial for industries that require rapid turnaround times.
- Material Versatility: A wide range of thermoplastic materials can be utilized in injection molding, offering manufacturers flexibility in choosing materials that best suit their product requirements.
- Enhanced Aesthetics: Injection molded components can be produced in a variety of colors and finishes, enhancing the visual appeal of the end product.
Applications of Injection Plastics in Metal Fabrication
Injection plastics find numerous applications across various sectors of metal fabrication, showcasing their versatility. Here are some prevalent uses:
1. Electrical and Electronics Components
In the electronics industry, injection plastics are used to create housings, insulators, and other components that require both durability and electrical insulation.
2. Automotive Industry
The automotive sector utilizes injection plastics for interior and exterior components, including trims, dashboards, and various brackets, which aid in reducing vehicle weight and enhancing fuel efficiency.
3. Medical Devices
In the medical field, injection plastics are essential for manufacturing components such as syringes, surgical instruments, and diagnostic devices, where precision and cleanliness are paramount.
4. Home Appliances
Home appliances frequently feature parts made from injection-molded plastics, enhancing product durability while ensuring aesthetic appeal.
5. Construction and Infrastructure
Injection plastics are used in construction for manufacturing pipes, fittings, and other components that require resistance to corrosion and weathering.
The Process of Injection Molding Explained
To further understand how injection plastics impact metal fabrication, let’s break down the injection molding process in detail:
Step 1: Material Selection
Choosing the right plastic material is crucial. Different applications require specific properties such as strength, heat resistance, and flexibility. Common materials include ABS, polypropylene, and polycarbonate.
Step 2: Mold Design
A well-designed mold is essential for high-quality production. The mold must accommodate the design specifications, including tolerances, undercuts, and draft angles which facilitate easy demolding.
Step 3: Injection Phase
In this phase, the molten plastic is injected into the mold under high pressure. The injection speed and pressure are critical and must be controlled to minimize defects.
Step 4: Cooling Phase
After injection, the plastic must cool and solidify. Cooling methods can vary significantly, affecting the cycle time and energy consumption of the process.
Step 5: Demolding
Once the part is cooled, the mold is opened, and the injection-molded part is removed. This step is where the precision and finish of the final product are revealed.
Challenges of Injection Molding in Metal Fabrication
While there are numerous advantages to using injection plastics, challenges do exist. Understanding these can help manufacturers mitigate risks:
- Initial Setup Costs: The cost of designing and manufacturing molds can be high, which may be a barrier for smaller manufacturers.
- Material Limitations: Not all plastics are suitable for injection molding, which can limit material choice for certain applications.
- Technical Expertise: A skilled workforce is necessary for managing the complexities of injection molding, from design to quality control.
Future Trends in Injection Plastics
The future of injection plastics in metal fabrication seems bright, with several trends shaping the landscape:
- Biodegradable Plastics: As sustainability becomes increasingly important, the development of biodegradable materials is expected to transform injection molding practices.
- Advanced Technologies: Techniques such as 3D printing in conjunction with injection molding are likely to emerge, enabling even more complex designs and faster prototyping.
- Smart Manufacturing: The integration of IoT (Internet of Things) technologies in the manufacturing process can lead to greater efficiency and quality control in injection molding.
- Recyclability: Enhancements in recycling technologies for used injection plastics are expected, promoting a circular economy and reducing environmental impact.
Conclusion
Injection plastics have revolutionized the field of metal fabrication, presenting unique advantages, numerous applications, and an optimistic future. Manufacturers like Deep Mould are at the forefront of this trend, leveraging technology to produce high-quality components that meet modern standards. Understanding this process and its implications is invaluable for industries aiming to innovate and stay competitive. The incorporation of injection plastics not only propels efficiency and precision but also aligns with sustainability goals that are increasingly central to enduring business practices.
As the industry continues to evolve, staying informed about developments in injection plastics will be crucial for metal fabricators and manufacturers alike, ensuring they harness these advancements to drive their business forward.