The Advantages of Plastic Injection for Electronics and Medical Supplies
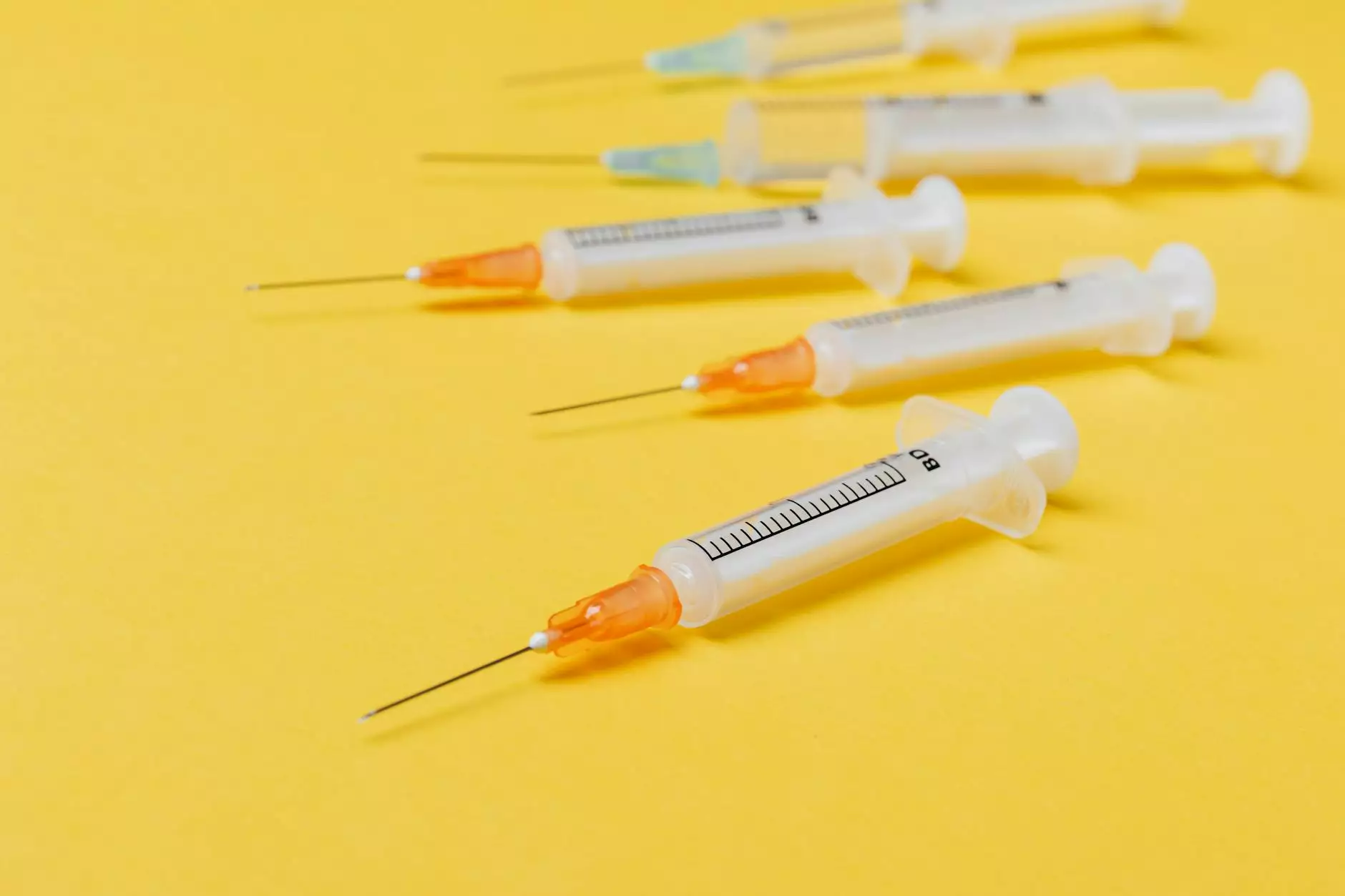
Plastic injection molding is a versatile and highly efficient manufacturing process that has transformed the way products are designed and produced in the electronics and medical supplies industries. Nolato, a reputable company with a strong presence in these sectors, offers cutting-edge plastic injection solutions that meet the highest standards of quality and precision.
Why Choose Plastic Injection for Electronics?
Electronics manufacturers rely on plastic injection molding for its unparalleled ability to create complex, intricate components with precision and consistency. With the advancement of technology, plastic injection has become the go-to method for producing high-quality parts for electronic devices, such as smartphones, tablets, laptops, and other gadgets.
Benefits of Plastic Injection in Electronics:
- Cost-Effective: Plastic injection allows for efficient mass production, leading to cost savings for electronics companies.
- Design Flexibility: Complex geometries and intricate details can be easily achieved in plastic injection molding, enabling innovative product designs.
- Material Variety: A wide range of materials can be utilized in plastic injection molding to meet the specific requirements of electronic components.
- Short Lead Times: Plastic injection offers fast production cycles, ensuring timely delivery of electronic products to the market.
- Quality Assurance: With Nolato's expertise in plastic injection, electronics manufacturers can expect superior quality and consistency in their products.
Plastic Injection in the Medical Supplies Industry
In the medical supplies sector, precision and reliability are paramount, making plastic injection molding an ideal choice for manufacturing critical components such as surgical instruments, medical devices, and laboratory equipment. Nolato's advanced plastic injection capabilities play a crucial role in meeting the stringent requirements of the medical industry.
Advantages of Plastic Injection in Medical Supplies:
- Biocompatibility: Medical-grade plastics can be used in injection molding, ensuring compatibility with human tissues and bodily fluids.
- Sterilization Capabilities: Plastic components produced through injection molding can withstand various sterilization processes required in healthcare settings.
- Tight Tolerances: Plastic injection allows for the production of precise and accurate parts, essential for medical devices and instruments.
- Regulatory Compliance: Nolato adheres to strict industry regulations and standards to ensure the safety and efficacy of medical supplies manufactured through plastic injection.
Conclusion
Plastic injection molding has revolutionized the electronics and medical supplies industries, offering unmatched precision, efficiency, and quality in the production of components and devices. By partnering with Nolato, a leading expert in plastic injection, businesses can leverage these cutting-edge technologies to stay ahead of the competition and deliver innovative solutions to their customers.
Experience the power of plastic injection with Nolato and elevate your electronics and medical supplies to new heights of performance and reliability.