Understanding High Pressure Tube Fittings: Essential Components for Superior Performance
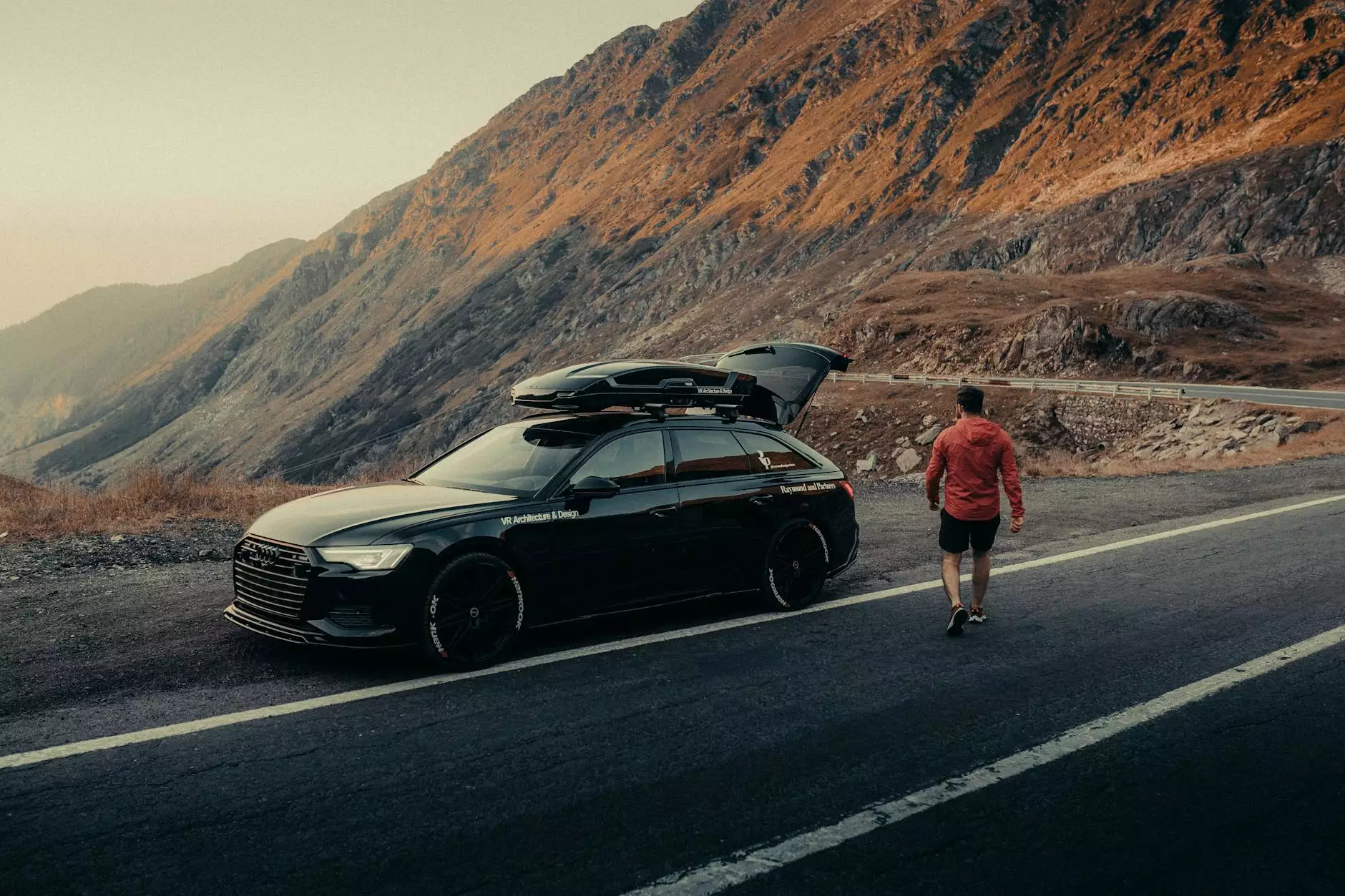
In the realm of fluid transfer and management, high pressure tube fittings play a crucial role in ensuring that systems operate safely and efficiently. These fittings are designed to endure and manage high pressure applications, making them indispensable in various industries. In this comprehensive guide, we will delve into the intricacies of high pressure tube fittings, their types, applications, and why companies should consider investing in top-quality fittings from reliable suppliers like fitsch.cn.
The Importance of High Pressure Tube Fittings
High pressure tube fittings are mechanical devices that connect sections of tubing or piping to facilitate the flow of liquids or gases under high pressure conditions. Understanding their importance is essential for any business that relies on fluid management systems. Here are several reasons why these fittings are crucial:
- Safety: High pressure systems can be dangerous if not managed properly. High quality fittings ensure that systems are securely connected, minimizing the risk of leaks and failures.
- Reliability: Using the right fittings guarantees a reliable connection that can withstand extreme conditions, thereby enhancing the overall performance of the system.
- Efficiency: Properly installed high pressure fittings reduce the chances of fluid loss and improve the efficiency of the system, which can lead to significant cost savings.
Types of High Pressure Tube Fittings
High pressure tube fittings come in various forms, each designed for specific applications. Understanding these types is essential for selecting the right fittings for your business needs. Here are the most common types of high pressure tube fittings:
1. Compression Fittings
Compression fittings are widely used in high pressure applications. They work by compressing a ring (the ferrule) onto the tube, creating a tight seal. This design helps handle high levels of pressure while providing ease of installation and removal.
2. Flare Fittings
Flare fittings are designed with a conical seating surface that allows for a secure connection. When the nut is tightened, it compresses the flared end against the fitting, creating a leak-proof seal. These fittings are ideal for applications requiring a strong and reliable connection under high pressure.
3. Butt Weld Fittings
Butt weld fittings are robust fittings created by welding the ends of two pipe sections together. These fittings are suitable for high pressure applications due to their durability and ability to withstand significant stress.
4. Socket Weld Fittings
Socket weld fittings are used to connect pipes in a high pressure system by inserting the pipe into a socket and welding it in place. This type of fitting is robust and minimizes the risk of leaks, making it a popular choice in industrial sectors.
5. Threaded Fittings
Threaded fittings have male and female threads that screw together to form a connection. While they are generally not recommended for very high pressure applications due to the risk of leaking, they can be used in certain situations where pressure is moderate.
Applications of High Pressure Tube Fittings
High pressure tube fittings are utilized across various industries, including:
- Oil and Gas: In the oil and gas sector, these fittings are used to transfer oil, natural gas, and other fluids under high pressure conditions.
- Aerospace: Aerospace applications require fittings that can endure extreme temperatures and pressures, making high pressure tube fittings ideal components.
- Hydraulics: Hydraulics systems operate on principles of pressure, and fittings must reliably contain the high pressure fluid used in machinery.
- Manufacturing: In manufacturing processes, high pressure fittings are essential for moving fluids and gases efficiently through different stages of production.
- Power Generation: In power plants, these fittings are crucial for managing steam and other high-pressure fluids in energy generation processes.
The Crucial Role of Material and Design
The effectiveness of high pressure tube fittings hinges significantly on the materials used in their construction. Common materials include:
- Stainless Steel: Renowned for its corrosion resistance and strength, stainless steel is a popular choice for high pressure applications.
- Carbon Steel: While less resistant to corrosion than stainless steel, carbon steel fittings are durable and suitable for various industrial applications.
- Plastic and Composite Materials: Some high pressure applications in specific industries use advanced plastics that can handle pressure while being lightweight and resistant to certain chemicals.
Additionally, the design of the fittings plays a vital role in their function. Fittings should be designed to accommodate thermal expansion, vibrations, and potential stresses from connected components. Ensuring compatibility with tubes and pipes is crucial to maintain integrity and functionality.
Selecting the Right High Pressure Tube Fittings for Your Business
When it comes to choosing the right high pressure tube fittings for your specific needs, consider the following factors:
1. Pressure Requirements
Understand the maximum pressure that your application will encounter. This will dictate the type of fitting material and design that is suitable for your needs.
2. Fluid Compatibility
Different fluids can interact with materials in various ways. Ensure that the fittings you choose are compatible with the fluids you plan to use, particularly if they are corrosive or have high temperatures.
3. Environment
Consider the environmental conditions where the fittings will be installed. Factors such as temperature, humidity, and exposure to chemicals can influence the durability of the fittings.
4. Installation Requirements
Some fittings may require specific tools for installation. Ensure that your team is equipped with the necessary tools and knowledge to install the fittings properly to avoid future complications.
Advantages of Sourcing from Quality Suppliers like Fitsch.cn
When it comes to sourcing high pressure tube fittings, choosing a reputable supplier is vital. Here are several advantages of sourcing from a trusted business like fitsch.cn:
- Quality Assurance: Established suppliers maintain strict quality control standards, ensuring that you receive reliable and durable fittings.
- Wide Range of Products: Reputable suppliers offer a comprehensive selection of fittings, suitable for various applications and industries.
- Expert Guidance: Trusted suppliers often employ knowledgeable staff who can provide valuable insights into selecting the right fittings for your needs.
- Cost-Effectiveness: Sourcing from a quality supplier can lead to competitive pricing, reducing your overall project costs.
Conclusion
In summary, high pressure tube fittings are vital components for businesses that depend on fluid management systems. By understanding their importance, types, and applications, businesses can make informed choices that enhance safety, reliability, and efficiency. Investing in high-quality fittings from reputable suppliers like fitsch.cn not only ensures superior performance but also showcases a commitment to maintaining safe and efficient operations. With the proper fittings in place, your business will thrive in today’s competitive marketplace, driving productivity and success.